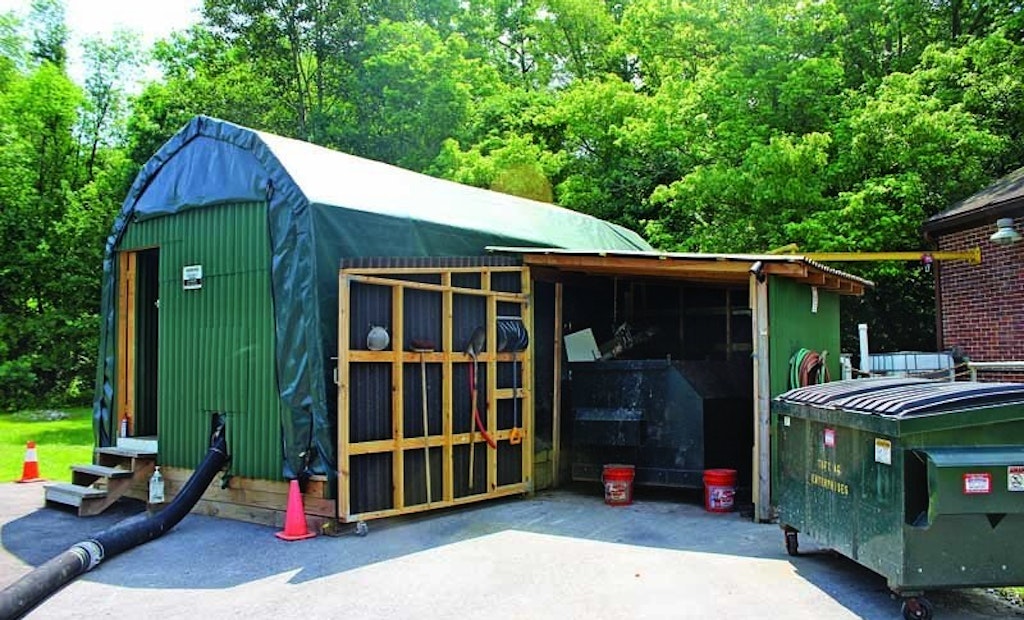
Interested in Dewatering/Biosolids?
Get Dewatering/Biosolids articles, news and videos right in your inbox! Sign up now.
Dewatering/Biosolids + Get AlertsIn Maryland’s Anne Arundel County, the proliferation of wipes in the sewers has created a problem beyond the clogging of pumps: disposal of the material once it is removed from lift station wet wells.
The mix of wipes, rags, plastics and other debris, along with grease, has to be suitably dry before it can be landfilled. In fact, such waste typically needs to pass a paint filter test, documenting that it contains no free water, before sanitary landfills will accept it.
Anne Arundel County was exploring ways to process its lift station wet well waste when Utilities Division staff members encountered Stephen Toft, who had been handling various mechanical contracting projects for the county.
Toft offered to build a prototype wet waste separator if the county would allow him to deploy and test it on its wastewater collections system. After about a year of testing, the device has reliably produced waste material suitably dry for landfill disposal.
Growth in non-dispersibles
Anne Arundel County, south of Baltimore and home to about 530,000, operates seven wastewater treatment plants and a collections system that includes 257 lift stations, according to David Watts, utility administrator.
“Within the last four to five years, we have seen a huge increase in the level of non-dispersible wipes in the system,” says Watts. “It has grown exponentially. We needed a way to get that material out of the system and dispose of it. We had the ability to pump it through and remove it at the headworks of the treatment plants. However, that was clogging pumps and air relief valves and causing overtime labor.”
The alternative was to use vacuum trucks to remove the material from the lift station wet wells, but that involved drying the material before landfilling. “We don’t have the privilege of large drying beds where we could dump the material and allow it to dry,” says Watts. “We could always find someone to take the grease, but we couldn’t find a way to process the wet well debris with plastics, rags and grease combined.”
The county had all its pump stations on a cleaning schedule, ranging from monthly to annual. Debris vacuumed was hauled to the largest pump stations, and from there pumped through to the treatment plants.
Designing a solution
Toft observed the debris accumulations in the wet wells and came up with the concept for a solution. “The county Utilities Division is a very progressive and innovative group,” he says. “I told them I thought I could solve the problem and would be willing to do it with my own money, but if I was going to build something, I had to be able to test it.
“I said, ‘Will you allow me to deploy my machine at one of your plants or lift stations and send your vacuum trucks to it? Everything will be at no charge. My promise is that if I make a mess, I’ll clean it up.’”
When the county staff agreed, Toft and his company, Old Line Environmental, went to work. In consultation with Watts, utility line superintendent Shawn Moulden and other division superintendents, Toft built a base unit. “We tested it and made several modifications until we came up with the prototype,” says Toft. “At that point, it worked pretty efficiently.”
The unit is deployed on a trailer at a major, centrally located lift station. It measures 6 feet high, 7.5 feet wide and 18 feet long; a portable enclosure and a shelter for a dump container occupy a total 25- by 30-foot space.
Simple process
The county operates two primary wet well vacuum trucks with 3,000-gallon tanks. On arrival at the waste separator, the truck driver connects to it with a standard 6-inch vacuum pressure line, then hoists the tank to a nearly vertical position. “The driver then opens the valve on the truck,” says Toft. “Our unit is equipped with a pneumatic valve that enables us to control the flow from the truck.”
The material first enters a rotary screen with different zones and flight configurations. Water and materials 1/8 inch and smaller pass through that screen into a wet sump. The water then flows to an oil/water separator that captures the floatable grease. All the wastewater then enters the lift station and is pumped on to the treatment plant.
The separated solid material is delivered to a custom-fabricated dewatering conveyor with compression rolls that squeeze the free water out. The dewatered material is conveyed to a 4-cubic-yard dump container, identical to those used at the treatment plants’ headworks. A front-load truck picks up the full container and carries it to the landfill.
An Old Line Environmental operator staffs the unit eight hours per day, Monday through Friday. “When the truck hooks up it’s just a matter of starting the unit with a couple of push-buttons,” says Toft. “The process is very visible and is easily adjusted based on the flow. In terms of electricity usage, our draw is normally 21 amps at 480 volts.”
The unit processes 150 to 200 gpm, and in its first nine months of operation separated 167 cubic yards of dewatered debris, according to Watts. The device is designed to also process septage and digester cleanings, although Anne Arundel County has not used it for those purposes.
Watts says the unit at a lift station about 75 yards from a townhouse community has drawn no odor or noise complaints. The main sound from the process comes at the end of the cycle when the truck operator turns on the vacuum briefly to draw out liquid from the hose.
“I understand from talking to the vacuum truck operators and the maintenance people that the process has cut down a great deal of emergency maintenance by preventing the damage the wipes and debris have done to the pumps,” Toft says.
Advancements planned
The device is now being re-engineered for commercial production. The commercial model will be about 4 feet longer than the prototype, at 22 feet, to enable greater throughput, Toft says. It will also be fully automated with a touch-pad system so that the truck drivers can use it without an operator on site.