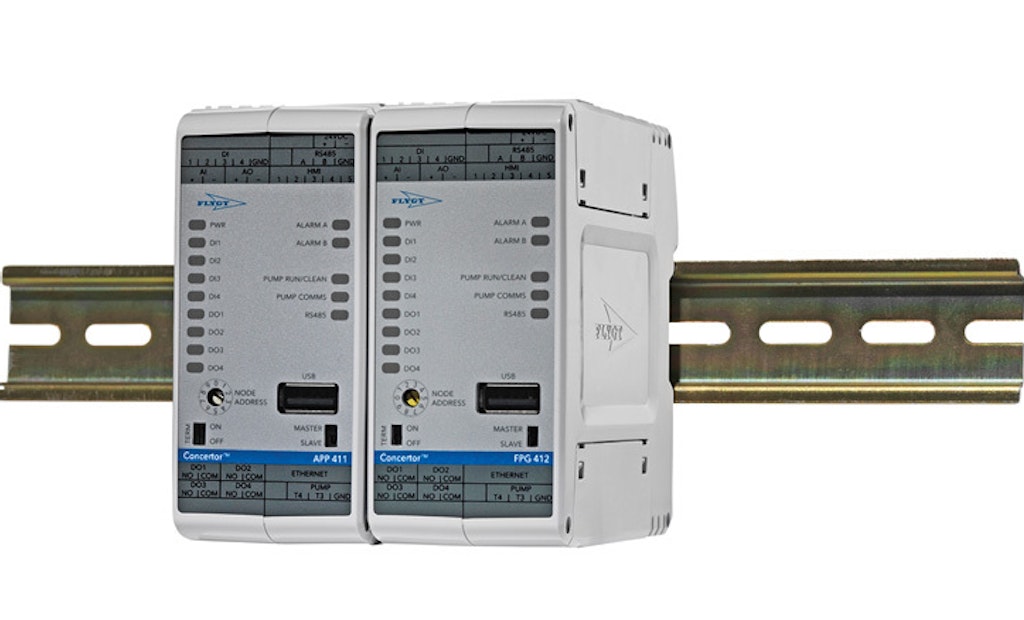
Wastewater pumping stations can be prone to pump clogging and inefficient energy consumption. They can also require frequent cleaning by way of waterjet/vacuum trucks.
Now Xylem has introduced the Concertor pumping system with integrated intelligence.
The system, from the...