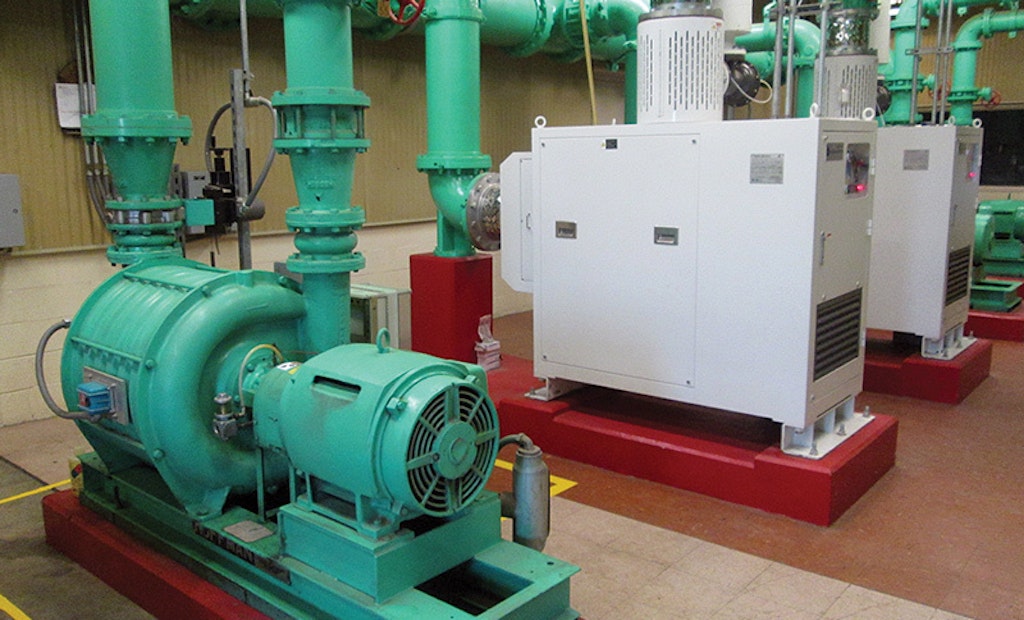
Sometime this year, officials in Gresham, Ore. hope to be generating all of the 15,000 kWh needed to run the city’s wastewater treatment plant every day. An expanded fats, oils and grease (FOG) program and a solar photovoltaic array are expected to save the plant about $570,000 a...