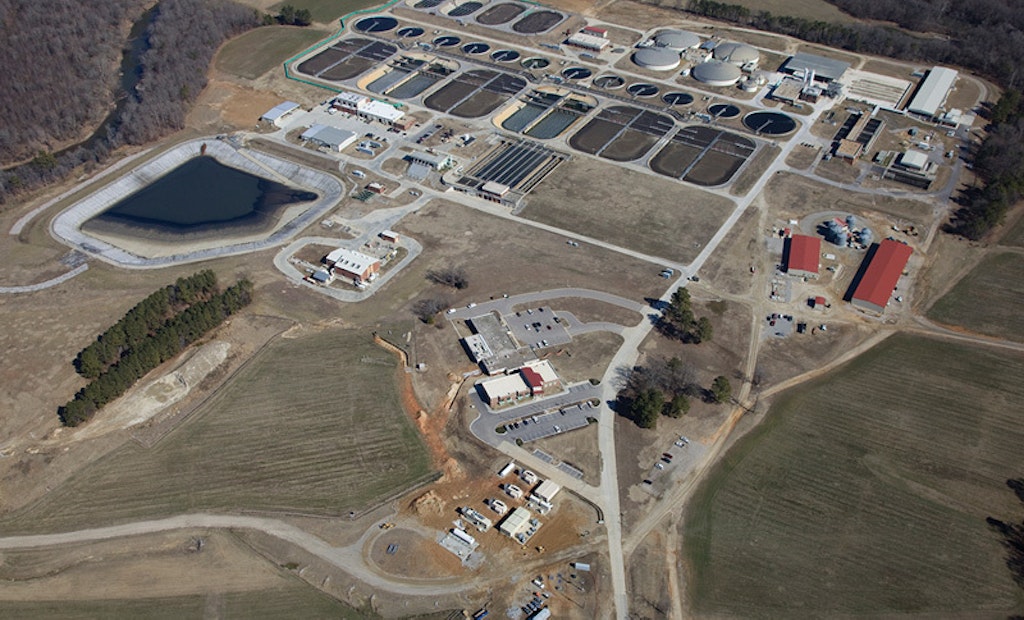
It is the picture of a sustainable system: nourishing crops with biosolids, converting crops into biodiesel, fueling engines to power a wastewater treatment plant, creating more biosolids. Such a closed system is being used at the Neuse River Wastewater Treatment Plant in...