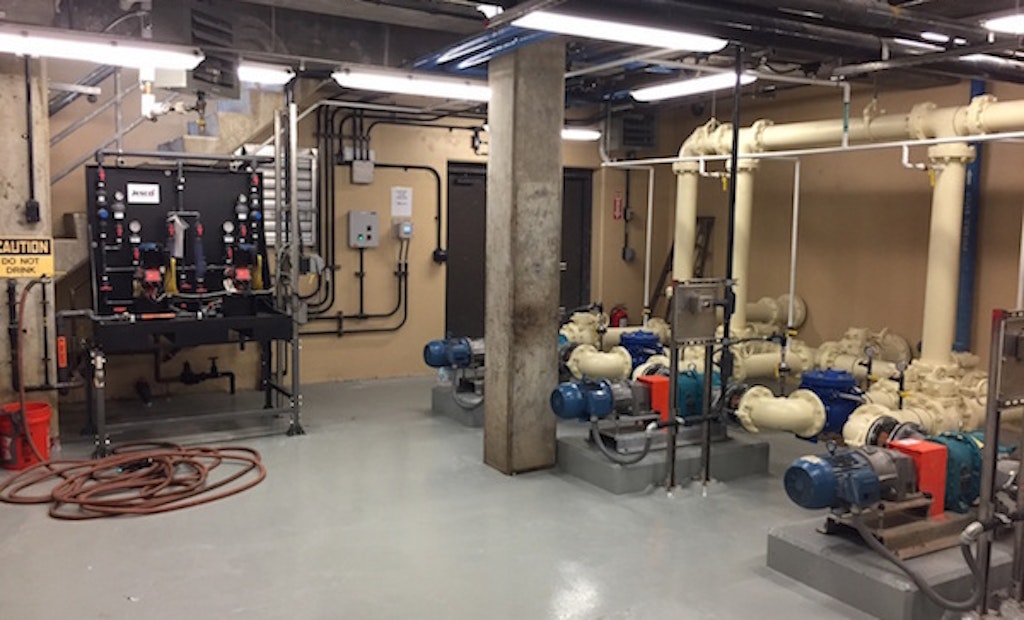
Treatment plants all over the country are modernizing at a rapid pace, and there will come a time in your career as an operator when you must adapt to survive. There’s a real temptation to resist change, but the operators who embrace new opportunities, learn new skills and strive...